While metal 3D printing is gaining popularity for its ability to fabricate complex metal shapes, there are still significant challenges, such as high production costs due to extensive post-processing requirements. Researchers at the University of Cambridge have developed a promising solution to this issue. They have introduced a novel metal 3D printing technique, initially tested on steel, which they argue surpasses the traditional method of heating and beating.
The conventional approach, heating and beating, involves hardening the material with a hammer and then softening it with heat. This technique, reminiscent of practices employed by historical blacksmiths, is less efficient compared to modern FDM metal 3D printing methods. Additionally, it is ill-suited for creating intricate parts. However, the new metal 3D printing process developed by the University of Cambridge researchers offers improved efficiency and is better equipped for fabricating complex components.
However, the enduring nature of these traditional processes stems from their ability to alter the internal structure of materials, thereby allowing precise control over their properties. Dr. Matteo Seita, leading the project at Cambridge’s Department of Engineering, emphasizes this point: "The reason why heating and beating is so effective is because it changes the internal structure of the material, allowing control over its properties. That’s why it’s still in use after thousands of years."
Yet, the limitations of conventional techniques may soon be addressed. The aim is to tackle a significant drawback of 3D printing methods: the inability to manipulate the material's internal structure as effectively. This limitation is particularly evident in metal 3D printing, necessitating post-processing such as heat treatment. By devising a method to regain this structural engineering capability without resorting to traditional heating and shaping methods, not only could costs be reduced, but the ability to control properties could also facilitate the utilization of the environmentally friendly aspects of 3D printing, as highlighted by Seita.
Creating a New Metal 3D Printing Process Superior to ‘Heating and Beating’
The researchers aim to enhance the appeal of metal 3D printing within the broader metal manufacturing sector through their innovative approach. Collaborating with teams from Nanyang Technological University, the Agency for Science, Technology and Research (A*STAR), the Paul Scherrer Institute, VTT Technical Research Centre of Finland, and the Australian Nuclear Science & Technology Organization, the Cambridge team has devised a meticulous process, termed a 'recipe', enabling precise control over the internal structure while 3D printing metal.
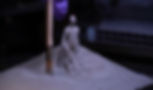