
Stainless Steel Metal 3D Printing- An Overview
Searching for the ideal metal 3D printing material? Stainless Steel 316L offers corrosion resistance and functionality for your parts. Discover essential information and tips to successfully 3D print your model in our Stainless Steel 316L (metal) material.
What is Stainless Steel 316L 3D Printing?
316L Stainless Steel printing is very accurate because of the fine coating resolution (30-40 µm) and the laser’s accuracy. Unlike polymer powder sintering, stainless steel printing through DMLS requires adding base structures in order to attach the part to the board and to strengthen distinctive geometries like overhangs. The bases themselves are made from the same powder as the piece and will be taken off afterwards.
With no particular finishing, the material gives off a granular and coarse appearance, though suiting most applications. Smooth and shiny surfaces can be acquired after printing through finishing steps. Pieces can be machined, drilled, welded, electro-eroded, granulated, polished, and coated.
​
Compared to the other metal 3D printing materials, stainless steel is the smoothest material.
3D printing process of Stainless Steel
Stainless Steel 3D printing utilizes fusion or laser sintering techniques, specifically DMLS (Direct Metal Laser Sintering) and SLM (Selective Laser Melting). DMLS involves a laser sintering process that fuses stainless steel powder layer by layer, bringing it close to its fusion point to create the desired object.
The high-temperature fusion of stainless steel in the additive manufacturing process demands extensive expertise in studying thermal and mechanical effects before the 3D printing stage. Additionally, a profound understanding of finishing techniques is essential for achieving the desired final product. This intricate process necessitates advanced technical skills and knowledge for successful stainless steel 3D printing.

The Power of Stainless Steel 3D Printing
Stainless steel, known for its corrosion resistance and heat tolerance, finds widespread use in everyday items, from cutlery to auto parts. Its versatility extends to 3D printing, where it excels due to being lightweight and cost-effective.
In various industries, 3D-printed stainless steel has become a go-to for manufacturing industrial components, as well as for creative endeavors in design and architecture. This approach proves advantageous, offering speed, cost-effectiveness, and efficiency compared to traditional manufacturing.
For those in need of stainless steel spare parts, prototypes, or tools, numerous printing options, materials, and services are available to meet diverse requirements.
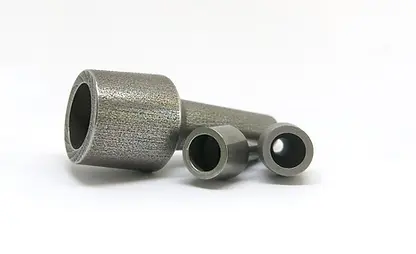
How to Metal 3D Printing Stainless Steel?
There are multiple methods for 3D printing stainless steel, each with its own advantages and drawbacks in terms of cost, speed, quality, and volume. The size of 3D printers varies from desktop models to large-scale units that can fill an entire room. The resulting stainless steel parts exhibit diverse mechanical properties, necessitating an understanding of the different printing methods to select the most suitable one for your project.
​
For instance, if you urgently require replacement nozzles for factory production, a desktop FDM printer may offer a quick and cost-effective solution. However, if your stainless steel components must endure specific levels of pressure and force, opting for technologies like laser powder bed fusion or metal binder jetting becomes essential. For large-scale items such as ship propellers, wire arc additive manufacturing (WAAM) is worth considering.
​
When evaluating stainless steel 3D printing options, factors to consider include final part density (ranging from 90% to 99%), porosity (which can be advantageous or disadvantageous depending on your application), and the required mechanical properties such as tensile strength.
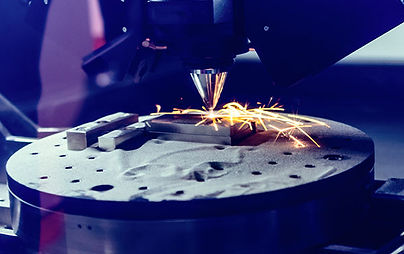
DMLS Stainless Steel 316L
316L Stainless Steel printing achieves high accuracy due to its fine coating resolution (30-40 µm) and the precision of the laser. In contrast to polymer powder sintering, DMLS stainless steel printing necessitates the addition of base structures for attaching the part to the board and reinforcing unique geometries such as overhangs. These bases, made from the same powder as the piece, are removed later.
​
The material exhibits a granular and coarse appearance without additional finishing, suitable for many applications. However, smooth and shiny surfaces can be obtained through post-printing finishing steps. The printed pieces are versatile, allowing for machining, drilling, welding, electro-erosion, granulation, polishing, and coating.


DMLS Stainless Steel 17-4
Stainless Steel 17-4 is an alloy renowned for its exceptional strength and hardness, crafted with 17% chromium and 4% nickel. The utilization of Direct Metal Laser Sintering (DMLS) ensures consistently superior mechanical properties and a refined finish characterized by fine layer heights. In its raw state, the part exhibits a granular texture with a matte appearance, yet it offers the flexibility for post-processing to achieve diverse finishes.
​
This alloy, combined with the DMLS technique, has found wide-ranging applications across industries such as aerospace, automotive, and medical devices. Its popularity stems from the ability to customize, exceptional corrosion resistance, and biocompatibility. Direct Metal Laser Sintering (DMLS) is particularly advantageous for fabricating small, intricate, hollow, or lattice structures, whereas simple, robust, or dense components may be more effectively produced through CNC machining.
Finishes of Stainless Steel 3D Printing
Stainless steel 3D printing produces parts with a density comparable to machined steel, allowing for similar machining and polishing processes.
Standard finishing involves removing support structures and medium-blasting the part surface for a uniform look.
For certain cases, features may undergo CNC machining or polishing, but this is determined on an individual basis.