What is Rapid Prototyping?
- Locanam 3D Printing
- Apr 23, 2024
- 5 min read
This new-age manufacturing technology allows for quick testing and refinement of products before hit the shelves.
Rapid prototyping is a 3d printing process of quickly creating physical models for computer-aided design (CAD) data using fast manufacturing techniques. This goal is to materialize an idea and move it from an initial concept to a work model as soon as possible
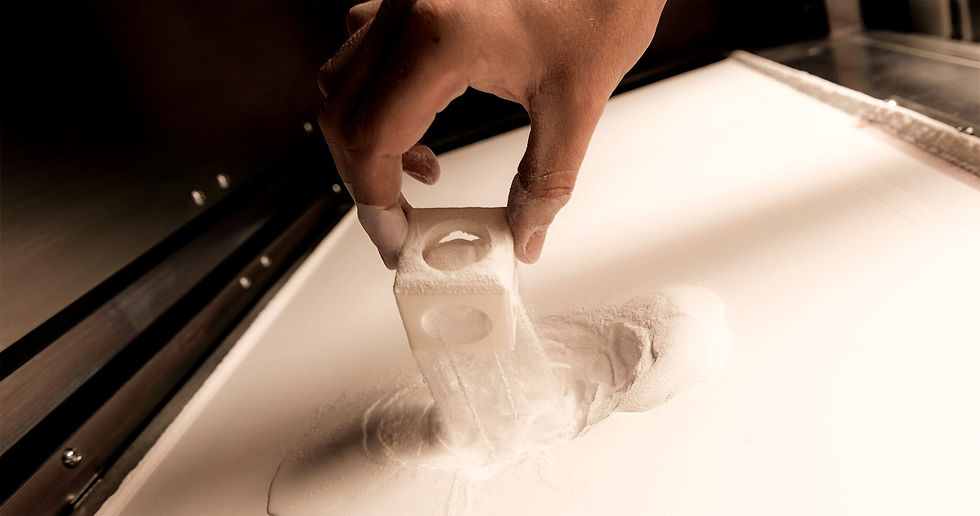
Rapid Prototyping definition
Rapid prototyping refers to an iterative method of fabricating sample products using a computer-aided design model. This process commonly involves additive manufacturing techniques, like 3D printing.
With rapid prototyping, engineers and designers possess the capability to refine prototypes iteratively, seamlessly transitioning between digital design iterations and physical fabrication. Consequently testing multiple versions of a sample model. This creates a near-instantaneous feedback loop and shortened product development cycles that validate a prototype’s viability on its way to becoming a finalized product.
Today, rapid prototyping is used across many industries, manufacturing everything from car parts and medical equipment to aerospace components.
What is Rapid Prototyping?
Before an item is set on a store shelf, it starts as a prototyping that undergoes months of development and experimentation. But thanks to 3D-printing technologies, rapid prototyping reduces that lifecycle to a fraction, with first iterations possible in a matter of time. “Rapid prototyping lets you turn ideas into something tangible, fast,” Paul Chow, chief technology officer and co-founder of tech review platform 3DGearZone, told Built In.
Since rapid prototyping allows for quick iteration, designers and engineers can test sample models, experiment to see what works then tweak the design before investing heavily in final production.
“Rapid prototypes might not be as strong or polished as final products,” Chow said. “One notable aspect is the opportunity it presents for early-stage exploration. You're essentially navigating the terrain before making extensive production commitments," explained Patrick Faulkner, a principal engineer at Accu, a prominent mechanical components manufacturer.
He emphasized that rapid prototyping fundamentally fosters iterative development, facilitating swift evaluation and adjustment processes. “This rapid method of information gathering shortens the product development cycle and in turn the whole project due to the ability to incorporate changes based on data and feedback from the objects produced in each round,” he said.
How Does Rapid Prototyping Work?
All prototyping starts as a digital file of a product design. They serve as a blueprint that instructs a 3d printer on how to build a structure layer by layer at a time.
Everything depends on the manufacturing approach, a heat source, or liquid binding may be used to fuse materials to print a three-dimensional model. As one layer cures, another is at the top until the design is fully materialized.
In the post-processing stage, the prototype is under the finishing touch such as removing all support structures and refining its surface. It proceeds to test, where it’s evaluated for functionality, form, and fit.
after collecting feedback from various sources such as in-house teams, collaborators partners, focus groups, stakeholders, and end users, the suggested alterations are incorporated into a fresh version of the design. This cycle continues until the prototype reaches its finalized form.
Rapid prototyping is an ongoing cycle of designing, printing, testing, and iterating. 3D printing can deliver a prototype in just a few hours, giving designers and engineers the opportunity to run tests, see how the design would work, and restart the cycle until the prototype is perfect.
Advantages of Rapid Prototyping
Producing prototypes rapidly offers multiple advantages
Speed
one of the major benefits of speed iteration and prompt development cycles is reduced time to market when building a prototype, from a matter of weeks to hours, like first iterations 3D printed in as little as a few hours.
Cost-Effective
The pace of rapid prototyping grants quick access to testing, where faulty, dead-ends discovered during the design or engineering phase of a prototype can be ruled out before deeper investment in materials, labor and machinery are made.
Reduced Risk
With prompt validation and concept testing, rapid prototyping helps reduced risks associated with product development, such as market acceptance and technical feasibility.
Better Designs
The quick pace and relatively low cost of rapid prototyping allows designers to produce and test multiple iterations of a design side-by-side, making way for creative experimentation as well as refinement. High-speed iteration leads to early feedback rounds, which can cue designers to identify and address potential issues sooner rather than later, leading to more informed decisions making.
Disadvantages of Rapid Prototyping
Look at the disadvantages of Rapid Prototyping
Accuracy
In rapid prototyping speed over accuracy. While high-fidelity mock-ups are possible, it is important to know that not all rapid prototyping methods are created the same. This is why designers may opt for more precise 3D printing practices, like stereolithography or material jetting, particularly when developing products that prioritize functionality.
Design Limitations
While 3D-printing devices may seem to be able to fabricate out of thin air, there's no assurance that every fine element of a sophisticated CAD design will survive professional-grade manufacturing methods by the time the prototype makes it to the final product stage.
Low Resolution
Depending on the chosen rapid prototyping technique, the surface finish and level of detail might not always match professional-grade industry standards. This may turn into additional post-processing steps to achieve the desired quality in surface finish, resolution quality, and sturdiness of a prototype.
Initial Cost
The initial setup cost required for rapid prototyping equipment can be high. Entry-level professional FDM 3D printers start at around $2,500. Those with a larger build are about $4,000, while the most advanced industrial FDM printers are upwards of $10,000.
Some Example of Rapid Prototyping
Fused Deposition Modelling (FDM)
FDM (fused deposition modeling) 3D Printing creates object parts by heating and extruding thermoplastics layer by layer. You can use FDM for fast prototyping and small-scale industrial manufacturing through Fused Deposition Modeling (FDM) 3D printing. While FDM is the most affordable 3D printing technology, Locanam is a Delhi-based FDM 3D Printing service provider. getting access to thermoplastics, including PLA, ABS, TPU, PETG, and PEI, and a dimensional accuracy of ±0.5% with a lower limit of ±0.5 mm.
Stereolithography (SLA)
Stereolithography (SLA) is an innovative method in additive manufacturing, specifically within the Vat Photopolymerization category. This technology is revolutionizing 3D printing by offering exceptional precision and flexibility for professionals across different sectors. Whether you're a professional looking for high precision or an enthusiast exploring the possibilities of 3D printing, SLA presents exciting opportunities.
Selective Laser Sintering (SLS)
SLS is a powder bed fusion 3D printing technology. In SLS (Selective Laser Sintering), a high-power laser draws each layer into a bed of powder, usually Nylon Powder. The laser sinters the powder particles together to form solid structures. Ones layer is complete, the build plate lowers slightly, and a powder recoater spreads new powder onto the previous layer. This technology is highly precise, with layer thicknesses typically ranging between 50 and 200 microns. Once the prints are complete, the machine operator must remove them, and powder can be recycled, and the printed pieces can be post-processed further via media blasting or media tumbling.
コメント