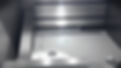
SLS 3D PRINTING | SLS 3D PRINTING SERVICE | AN OVERVIEW
SLS 3D Printing is an advanced cutting-edge technology that utilizes a high-powered laser to fuse material layers, enabling the rapid production of prototypes and small batches. Locanam specialize in SLS 3D Printing services to create end-use parts in Nylon powder beds, ensuring strong and good quality precision. Easily source high-quality parts for both prototyping and production through the help of Selective Laser Sintering (SLS) 3D printing technology.
In the domain of SLS 3D printing, the synergy of precision and creativity is paramount. This advanced technique uses a laser to accurately guide the creation of three-dimensional structures, layer by layer. The method capitalizes on plastic powder particles as the main material, expertly orchestrating their controlled fusion. The process is initiated by gradually heating the powder in the printing bed, ensuring the laser's capabilities are maximized without exceeding the material's melting point.
The following steps involve the machine gently spreading a fine layer of powder onto a platform. Directed by computer instructions, the laser carefully heats and fuses the powder at precise points. As each layer is added and the platform lowers, the object gradually takes shape until it is fully formed. Essentially, SLS (Selective Laser Sintering) is an advanced 3D printing technique where a laser acts as a skilled craftsman, melting plastic particles to create detailed objects with precision. This process, managed by a specialized SLS 3D printer, exemplifies the combination of technology and high quality in additive manufacturing.
Selective laser sintering (SLS) is a 3d printing and additive manufacturing process that uses high-powered lasers to sinter, or bind, finely powdered material together into a solid structure. In this process, a printer lays down an even layer of powder and then precisely sinters that layer, repeating the deposition and sintering process until the part is complete. The shape of the object is created by aiming a laser at the powder bed in specific points in space, guided by a digitally produced CAD (computer-aided design) file.
SLS printing primarily harnesses nylon as its key material, providing a versatile array of infills that enhance material properties. Whether it's the robustness of carbon-filled compositions or the flame-retardant characteristics, SLS materials are customized to cater to a variety of project requirements.
​
In the Field of additive manufacturing in layer technology, SLS utilizes a high-power laser, such as a carbon dioxide laser, to fuse tiny plastic powder particles into a solid structure, creating the intended three-dimensional form. The laser meticulously fuses powdered material by scanning cross-sections derived from a 3D digital representation of the part—sourced from CAD files or scan data—onto the surface of a powder bed. With each cross-section scan, the powder bed descends by one layer thickness, a new layer of material is added, and the selective laser sintering process is repeated until the part is completed.
How to Design Parts for SLS 3D Printing
Use the 3D Printing Design Guidelines to help you design your parts for machining. Once you have your designs ready, export them in an STL format. Ready to submit your designs? Go ahead and do so now to receive a FREE quote. Our team of 3d printing experts is always here to help you in every step, ensuring your parts are set for printing. We always provide support and recommendations.
Locanam SLS 3D Printing Services
Welcome to the Locanam cutting-edge Selective Laser Sintering (SLS) 3D printing Delhi, a revolutionary additive manufacturing technology that has transformed the landscape of creating precise and strong parts suitable for end-use, low-volume production, and rapid prototyping. highly honored for its cost-effectiveness in industrial 3D printing services, SLS sets itself apart by facilitating bulk production without the necessity for support structures.
SLS printing primarily harnesses nylon as its key material, providing a versatile array of infills that enhance material properties. Whether it's the robustness of carbon-filled compositions or the flame-retardant characteristics, SLS materials are customized to cater to a variety of project requirements.
​
In the Field of additive manufacturing in layer technology, SLS utilizes a high-power laser, such as a carbon dioxide laser, to meld minuscule particles of plastic powders into a cohesive mass, sculpting the desired three-dimensional shape. The laser meticulously fuses powdered material by scanning cross-sections derived from a 3D digital representation of the part—sourced from CAD files or scan data—onto the surface of a powder bed. With each cross-section scan, the powder bed descends by one layer thickness, a new layer of material is applied, and the selective laser sintering process repeats until the part reaches completed. A journey where precision seamlessly meets efficiency—uncover the limitless possibilities of SLS 3D printing for all your manufacturing needs.
How SLS 3D Printing Works
Selective Laser Sintering (SLS) is a 3D printing technique that uses powder bed fusion. In SLS, a high-power laser draws each layer into a bed of powder, usually Nylon Powder. The laser sinters the powder particles together to form solid structures. Once the layer is complete, the build plate lowers slightly, and a powder recoater spreads new powder onto the previous layer. This technology is highly precise, with layer thicknesses typically ranging between 50 and 200 microns. Once the prints are complete, the machine operator must remove them, and powder can be recycled, and the printed pieces can be post-processed further via media blasting or media tumbling.
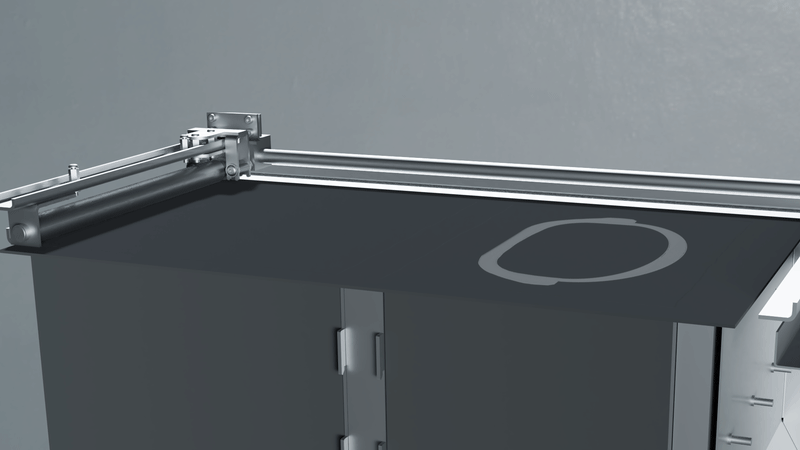
Applications of SLS 3D Printing
SLS 3D printing, with its remarkable versatility and precision, has made a significant impact in a diverse range of industries. This innovative technology has unlocked a multitude of possibilities and applications. Let's delve into some of the key sectors where SLS 3D printing service have found remarkable applications.
SLS 3D Printing In Aerospace
SLS 3D printing in the aerospace sector to produce lightweight and resilient components essential for spacecraft, satellites, and aircraft. This technology's capability to fabricate intricate, tailor-made parts guarantees high performance in these applications
SLS 3D Printing In Automotive
Automotive manufacturers leverage the capabilities of SLS 3D printing to fabricate tailor-made, high-performance components like intake manifolds, engine covers, and brake calipers. These parts not only enhance vehicle performance but also contribute to improved aesthetics.
SLS 3D Printing In Medical
SLS 3D printing technology is a valuable asset to the medical field, as it enables the production of extremely precise, patient-specific medical devices. Such applications encompass prosthetics, implants, and surgical tools, all of which play a role in enhancing patient outcomes.
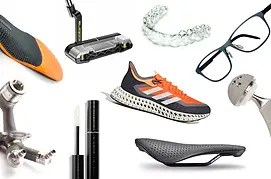
SLS 3D Printing Consumer Goods
From jewelry to fashion accessories and home decor items, SLS 3D printing service allows for the creation of highly detailed and customized consumer goods. Consumers can enjoy personalized products tailored to their preferences.
SLS 3D Printing Materials
Selective Laser Sintering (SLS) is a state-of-the-art 3D printing technology that frequently utilizes nylon, a versatile engineering thermoplastic, as its primary material. As a member of the polyamide family, nylon excels in functional prototyping and end-use manufacturing due to its exceptional properties.
SLS 3D printing Delhi with nylon yields components characterized by remarkable strength, stiffness, and durability, rendering them resistant to impacts and wear. The durability of nylon extends across diverse environmental factors, including UV radiation, light, heat, moisture, solvents, temperature fluctuations, and water exposure. Notably, 3D-printed nylon parts may demonstrate biocompatibility and non-sensitizing properties, broadening their applicability to diverse fields.
​
Nylon showcases remarkable versatility across various uses, ranging from engineering consumer products to innovative healthcare solutions. Enhanced versions like Nylon 12 and 11 benefit greatly from reinforcement with glass or carbon fiber, resulting in composite materials that offer exceptional strength and rigidity tailored to specific needs.
​
Beyond nylon, SLS 3D printers excel in crafting parts from flexible Thermoplastic Polyurethane (TPU). TPU seamlessly combines high tear strength and elongation at break characteristics typical of rubber materials with the design freedom and ease of SLS 3D printing Delhi. TPU emerges as an optimal choice for manufacturing flexible prototypes and end-use parts capable of withstanding daily use. It offers unparalleled design flexibility while ensuring durability and functionality.

Polyamide 12/(PA 12)
Durable PA-12 thermoplastics are incredibly versatile, making them an excellent alternative to traditional injection-molded items. They come in food-grade, medical-grade, and flame-retardant varieties.

Polyamide 11/(PA 11)
Durable Polyamide 11 thermoplastics provide exceptional impact resistance, making them well-suited for demanding applications. Their excellent performance in snap-fits and living hinges ensures.

Filled nylon/(PA)
These materials incorporate glass, aluminum, or mineral fiber fillers to deliver a diverse range of advanced characteristics, including enhanced stiffness, temperature resistance, strength, and surface quality.

Castable Polystyrene
Ideal for sacrificial patterns in the production of prototype metal castings and well-suited for low to medium production runs, eliminating the necessity for tooling.

ElastomericThermoplastics
Exhibiting a rubber-like flexibility combined with excellent memory, tear resistance, and abrasion resistance, this material is ideal for both prototypes and production parts.
The Process of SLS in Additive Manufacturing
A designer starts by creating a 3D model using a Computer-Aided Design (CAD) program. This model is sliced into thin layers, which are then sent to a Selective Laser Sintering (SLS) printer. In the printer, a leveling roller spreads a layer of powdered material on the build platform. A CO2 laser then traces a cross-section of the design, heating and fusing the powder into a solid layer. After each layer is fused, the build platform lowers to accommodate the next layer of powder. This cycle repeats, with unused material being recycled, until the entire part is formed.
Benefits of SLS 3D Printing
Investigating the advantages of SLS 3D printing reveals many significant benefits that position this technology as a revolutionary force within 3D printing manufacturing.
No support structures
Unlike some other 3D printing processes, the part does not need any support structures since empty spaces are filled with unused loose powder making it self-supporting.
This allows you the freedom to design empty hollow spaces, overhanging features, and very thin features. It means you can design parts with complex internal components or channels without the fuss of support structures (be sure to consider design guidelines though, to ensure proper removal of remaining powder). If you need a complex design, it is a good option and you don’t need to produce multiple parts to achieve this.
High productivity
The process is one of the fastest 3D printing technologies since the lasers have a fast-scanning speed and the powders used only need a short exposure for fusing. In addition, we can tightly arrange multiple parts in the chamber with minimal clearance to maximize the available build space – so you get more parts produced faster.
Excellent mechanical properties
The SLS process produces very strong adhesion between layers so parts have good isotropic properties. This means that their tensile strength, hardness, and elongation to break are similar across the x, y, and z axes.
These properties mean that the printed parts are often a good alternative to injection molded parts – whether for prototyping or to produce low volumes. Because of the materials used, generally Nylon, the parts also offer good chemical resistance.
Reduced product development time
All 3D printing technologies selective laser sintering allows engineers to prototype parts cost-effectively early in the design cycle since it does not require tooling and involves minimal setup.
Why Choose SLS 3D Printing Over FDM 3D Printing
Every 3D printing method boasts unique advantages, limitations, and prerequisites, catering to diverse applications and industries. FDM, while offering cost-effectiveness, exhibits lower precision and resolution compared to SLA or SLS technologies, making it less optimal for intricate designs. However, post-processing techniques such as chemical treatments or mechanical refinements can enhance surface quality and detail for more refined outcomes.
Best SLS 3D Practices
Is SLS 3D printing the optimal choice for your specific part or project? Consider the following guidelines:
​
Material Compatibility: SLS is adept at producing functional parts using a wide array of engineering plastics, with Nylon (PA12) being the most commonly used material.
Build Volume: The standard build volume for an SLS system typically measures 300 x 300 x 300mm.
Mechanical Properties: SLS-produced parts demonstrate commendable mechanical properties and isotropic behavior. For components with specialized requirements, additive-filled PA powders are readily available.
If you're prepared to move your parts into production, Locanam offers a convenient platform. Visit Locanam to obtain an instant quote and explore our onboard DFM analysis. For additional information, feel free to contact us at info@locanam.com.
Design Rules In SLS 3D Printing Service
Minimum Wall thickness: 0.8 – 1 mm
​
Minimum details size: 2.5 mm (for text/ hole diameters etc)
​
Layer thickness: 0.08 mm – 0.1 mm
​
Standard Accuracy: ± 0.3% (with lower limit on ± 0.3 mm).
​
Lead Time: Minimum 2-3 working days for dispatch
​
Surface finish: Grainy matt finish
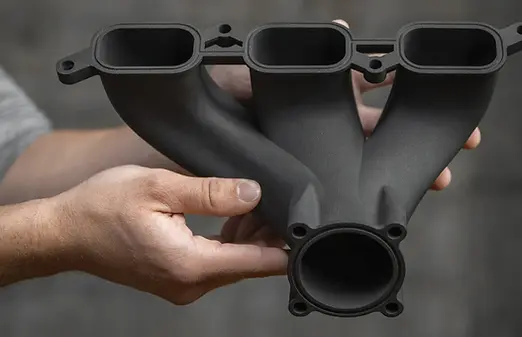
Post Processing
Basic: Powder removal, Bead blasting
Add on: Primer, Coating/ Painting
Why Choose Locanam For SLS 3D Printing Services
Locanam is a Delhi based 3d printing/prototyping service provider, offers all types of 3D Printing Services that set the standard for excellence service. Equipped with state-of-the-art SLS 3D printing technology, our service ensures the delivery of top-notch results.
Our focus on efficiency is demonstrated through our ability to swiftly produce high-quality 3D-printed objects using premium nylon materials. This makes Locanam the preferred choice for clients seeking superior parts that blend quality with cost-effectiveness.
At Locanam, we take pride in our quick turnaround times, enabling you to meet project deadlines seamlessly. Our streamlined processes and advanced technology ensure a hassle-free experience for all your 3D printing requirements. Choose Locanam 3D Printing for outstanding results, unparalleled quality, and a reliable partnership in your ventures.